فهرست مطالب
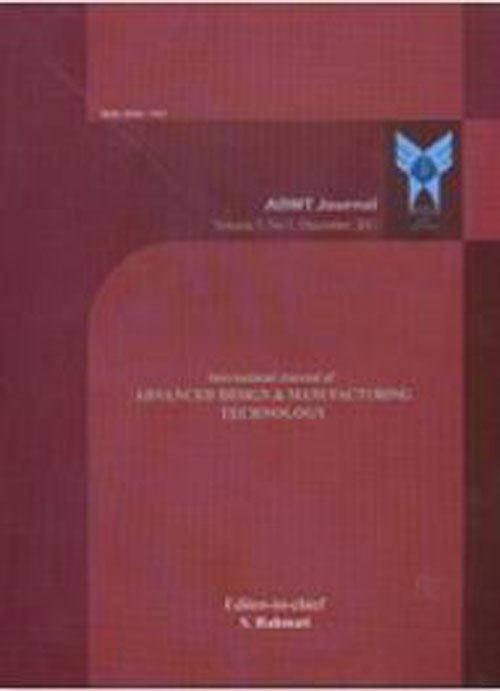
International Journal of Advanced Design and Manufacturing Technology
Volume:15 Issue: 1, Mar 2022
- تاریخ انتشار: 1400/12/10
- تعداد عناوین: 15
-
-
Pages 1-9
Nowadays grid structures are considered as one of the most useful composites because of their various applications. Since grid structures are vulnerable to impact loads, they should be investigated under such loadings. The present paper studies the low-velocity impact loading of sandwich panels with grid-stiffened cores using both experimental and numerical simulations. In addition to the impact behaviour and the resultant damage of the sandwich panels, the behaviour of these structures under three-point bending was studied before and after the impact loading. The results were provided for impact and bending loadings separately. Then the effect of impact loadings on bending strength was investigated and it was found that the impact loading decreases the bending strength. A consistency between numerical and experimental results was also observed, which confirms the applicability of the Finite Element Method (FEM) in simulating the behaviour of such structures under impact and bending loads, while saving lots of time, efforts and costs.
Keywords: Composite, Finite Element Method, Grid Structures, Sandwich panels -
Pages 11-19
In this study, the micro electro-polishing method was employed to improve the surface quality of microbeams machined by the micro WEDM method and to remove the recast layer. This approach changes the dimensions of the microbeams, as a result of the electrochemical corrosion, in addition to the elimination of the recast layer. To diminish the impact of this process on the dimensional deviation of the fabricated microbeams, the influence of the micro electro-polishing process parameters such as voltage, duration, cathode diameter, and electrolyte composition on the dimensional deviation of microbeams was studied using the Taguchi method. The optimum values of process parameters were determined by the S/N ratios analysis, and the order of parameters importance was determined through analysis of variance of the S/N ratios. It was found that the optimal levels of the process parameters are voltage of 2 V, process duration of 20 s, cathode diameter of 50 mm, and electrolyte composition of 25-5-40 ml (sulfuric-phosphoric-water) within the range of experiments. By using the optimum values of the parameters, the dimensional deviations were found to be 5.23 times lower compared to the average of the results. The importance of process parameters was found to follow this order: electropolishing duration, electrolyte composition, cathode diameter, and process voltage.
Keywords: Microelectromechanical Systems, MEMS, micro WEDM, micro polishing, micro electropolishing, wire electrical discharge machining -
Pages 21-28
In this paper, a Mindlin rectangular nanoplate model is developed for the bending and vibration analysis of a graphene nanoplate based on a modified couple stress theory. In order to consider the small scale effects, the modified couple stress theory, with one length scale parameter, is used. In modified couple stress theory, strain energy density is a function of strain tensor, curvature tensor, stress tensor and symmetric part of couple stress tensor. After obtaining the strain and kinetic energy, external work and substituting them in the Hamilton’s principle, the main and auxiliary equations of the nanoplate are obtained. Then, by manipulating the boundary conditions the governing equations are solved using Navier approach for bending and vibration of the nanoplate. The bending rates and dimensionless bending values under uniform surface traction and sinusoidal load and different mode frequencies are all obtained for various plate's dimensional ratios and material length scale to thickness ratios. The effect of material length scale, length, width and thickness of the nanoplate on the bending and vibration ratios are investigated and the results are presented and discussed in details.
Keywords: Bending, Modified couple stress theory, Mindlin nanoplate, Navier's Solution, Vibration -
Pages 29-50
This study investigates the fatigue life of a cracked plate subjected to cyclic load under linear elastic fracture mechanics, using a numerical method of extended isogeometric analysis (XIGA) with a K-refinement approach. XIGA is applied to simulate discontinuity problems without meshing and without the necessity for element boundaries to be aligned to crack faces. In this method, the crack faces are simulated by discontinuous Heaviside functions, whereas the singularity in the stress field at the crack tip is simulated by crack tip enrichment functions. The stress intensity factors for the cracks are numerically calculated using the interaction integral method. Paris law of fatigue crack growth is utilized for predicting the fatigue life of a cracked plate. In the standard finite element analysis, there is no refinement method similar to k-refinement. The effect of the k-refinement on the accuracy of the values stress intensity factor and fatigue life is investigated. To achieve this, the order of Non-uniform rational B-Splines (NURBS) basic function is considered as linear, quadratic, and cubic. It is observed that as NURBS orders are increased in k-refinement, results are improved, and the error is lower compared with the analytical solution. The results show that values of stress intensity factor and fatigue life obtained using XIGA are more accurate compared to those obtained by the finite element method. In addition, and they are closer to the results of the analytical solution, and the XIGA method is more efficient.
Keywords: crack growth, extended isogeometric analysis, Fatigue Life, k-refinement, NURBS -
Pages 51-63
In this paper, a joint position-force controller is used to control a 6R general-purpose robot manipulator. The manipulator comes into interaction with a spherical object in a numerically simulated environment. A controller has been implemented using the MATLAB Simulink software which uses the Simmechanics second-generation toolbox. A useful numerical contact model is used for modelling the interaction between the manipulator’s end-effector and the environment which generates the interaction feedback forces. The control algorithm presented in this paper is developed in the Cartesian space and the original control algorithm was modified to satisfy the desired input position in the base coordinate frame. The control algorithm was verified using a virtual environment, before hardware implementation. The novelty of the controller is determining the input tactile forces for the robot without actually causing a collision between the end-effector and the object in the environment which can lead to fracture and damage to the environment or the manipulator. The modeling process of interaction with the spherical environment was investigated using Simmechanics to model precise mechanical characteristics of manipulator that are unknown to the designers and provide a great advantage in the simulation for them. The considered position and tactile force were tracked successfully with good accuracy. The results show that the proposed manipulator system controls the position and force with more than 95% accuracy and the accuracy of desired tracing trajectory is 99%.
Keywords: force control, Multibody Simulation, Simmechanics, Tactile Control -
Pages 65-71
In this work, Diamond Like Carbon (DLC) thin films were deposited on aluminum alloy 6061 by Plasma-Assisted Chemical Vapor Deposition (PACVD). Nitiding prior to coated leads to appropriate hardness gradient and it can greatly improve the mechanical properties of the coatings. The composition, crystalline structure and phase of the films were investigated by Grazing Incidence X-ray Diffraction (GIXRD). Atomic Force Microscopy (AFM) and Scanning Electron Microscopy (SEM) were employed to observe the morphology and structure of the film. The DLC layer exhibited a columnar structure. The adhesion force between the film and the aluminum alloy 6061 was 30.8 Mpa. The DLC film was determined by the pull of test. The hardness of the DLC film was 12.75 Gpa. The improvement of the adhesion DLC was attributed to a less gradient hardness configuration. In addition, the mean friction coefficient of the films was about 0.2 determined by nanoindentation test. According to the results, the high and unique hardness of this coating leads to increase of the wear resistance and thus the useful life of parts.
Keywords: DLC, PACVD, Thin Film, Tribology -
Pages 73-83In this paper, the analytic model of the mutation dynamics related to the cancer cells which is under the control of chemotherapy is developed and its corresponding metastasis is controlled using chemotherapy method. The progress of a cancer tumours is contributed to two main factors including metastasis and mutation. It is observed that controlling the metastasis dynamic without considering the mutation phenomenon is doomed to fail. In this paper, the mathematical model of the cancer dynamic is improved considering the mutation of the stem cells and the effect of chemotherapy injection as the corresponding controlling signal is investigated in the extracted state space. Controlling the cancer growth and its mutation process is accomplished here using PID controller and State Feedback Control (SVFC) method. It is shown that by the aid of the proposed model of this paper, not only the number of the cancer cells can be converted to zero, but also the mutation process can be blocked since the feedback of the mutated cells are also engaged in the state space of the system. Verification of the model is conducted by the aid of simulation in the MATLAB and comparing the results with previous studies.Keywords: Cancer Modelling, Dynamics of mutation, Metastasis Controlling, Stem-cells
-
Pages 85-94In this research, the effect of CaCO3 nanoparticles was experimentally investigated on vibrational damping behavior and static mechanical properties of polypropylene (PP). Hammer tests along with modal analysis were carried out to evaluate the forced vibration behavior of composite plates under one edge clamped support conditions while tensile tests were performed to assess the static mechanical properties. A comparison of the results showed an increment in the static mechanical properties of nanocomposites by increasing the nanoparticles content in the PP matrix. Composite with 10 wt.% nanoparticles showed the highest rise in Young’s modulus (39.71 %) compared to pure PP. An increment in Young’s modulus and stiffness led to an increasing trend in the damped natural frequencies of the nanocomposites so that the composite with 10 wt. % nanoparticles showed the highest damped natural frequency augmentation (23.6 %, 36.78 %, and 252.62 %) compared to pure PP in the first three modes. In addition, an enhancement in the nanoparticles content of the PP matrix led to an increasing trend in damping ratios of the nanocomposites such that the composite with 10 wt. % nanoparticles in the first mode (28.99 %) and composite with 7.5 wt. % nanoparticles in the second and third modes (418.66 % and 9.93 %) showed the highest rise in damping ratio compared to pure PP. Increasing damping ratios can be due to the proper dispersion of nanoparticles in the matrix and consequently energy dissipation of the stick-slip mechanism between the matrix and nanoparticles. Moreover, high nanoparticle contents had destructive effects on both the static and dynamic behavior of the composites.Keywords: calcium carbonate nanoparticles, Forced vibration, Modal Analysis, nanocomposite
-
Pages 95-107The purpose of the present paper is to investigate the effect of the second invariant of the deformation tensor on the axial and azimuthal shear deformation of an incompressible hyperelastic solid with various strain energy functions. To this end, the axial shear deformation of an incompressible cylinder with the modified Gent-Thomas, Gent-Thomas, Gent-Gent, and Carroll strain energies subjected to an axial shear traction is considered, where the displacement field is determined analytically for the first three models and numerically for the fourth model. The phenomenon of strain hardening at large elastic deformations, predicted either by the limiting chain extensibility condition for the modified Gent-Thomas and Gent-Gent models or phenomenologically by the Carroll model, is observed and it is shown that the second invariant of deformation increases the strain hardening experienced by such materials. Next, the azimuthal shear deformation of an incompressible annular wedge with the modified Gent-Thomas, Gent-Thomas, Gent-Gent, and Carroll models is considered, where the annular wedge is subjected to a controllable azimuthal shear deformation and the angular displacement is determined analytically for all the above models. Again, the second invariant of the deformation tensor is shown to have a significant effect on the azimuthal shear deformation as reflected in the increase of the strain hardening of the material in such deformation. In addition, the annular wedge with the modified Gent-Thomas and Carroll models is shown to have a higher resistance in azimuthal shear deformation than the other models mentioned above.Keywords: Axial shear, Azimuthal shear, Strain hardening, Controllable deformation, Incompressible hyperelastic solids, Second invariant of the deformation tensor
-
Pages 109-114Welding is known as one of the most popular attaching methods for different hollow section components. However, local concentrated heating, distortion, and residual stresses at welded joints are unavoidable. In this article, the welding simulation for rectangular hollow (RHS) sections for the front axle carrier of the new BMW series-7 is discussed and weld distortion and residual stresses in its aluminum T-joint for one proposed sequence are investigated. Comparisons of the results of this paper for this recommended sequence with experimental results in some references show good agreement and indicate that characteristics of the welding distortions are fully forecasted. In the following of this paper, the Finite Element Method (FEM) is used to offer a better sequence with smaller weld distortion and residual stresses. Weld distortion and residual stresses are highly influenced by welding strategy. In the proposed strategy, the needed time to perform the welding process decreased, and the total weld distortion and residual stresses decreased by 24% and 4%, respectively.Keywords: Finite Element Method, Hollow Section, Residual stresses, Welding Distortion, Weld Sequence
-
Pages 115-124The present study investigates the production process by closed die forging method of one of the sensitive and safe parts of KIA car brake, which is affected by various mechanical and thermal stresses in its operating conditions; therefore, in the present research, the application of this forming method in the Iranian automotive industry has been discussed. In this study, an attempt was made using finite element analysis in ABAQUS software to determine the maximum force required for forging this part. In addition, the influence of various parameters such as the temperature of the part during the forming process, the coefficient of friction between the part and the die, as well as the strain rate have been investigated. The results indicated that the friction coefficient has a significant effect on the maximum required force, and the maximum values of the load increase with increasing the friction coefficient; but the remarkable result is that the effect of this coefficient is negligible from a value onwards. This point is consistent with the observations in practice. Besides, a strong dependence of the results on the loading speed was observed, and the required force has increased with increasing loading speed for reasons such as the strain hardening phenomenon. Also, the force required for forging has decreased with increasing the temperature, which is due to reduced material strength. This reduction from 900°C to 1000°C is less than 2%, while it is approximately 40% from 1000°C to 1100°C, which is consistent with the experimental reports.Keywords: Hot forging, Finite Element Simulation, Loading Rate, Friction Coefficient, temperature
-
Pages 125-132The optimal position and minimum stiffness of an intermediate support is implemented to maximize the fundamental natural frequency of a vibrating cantilever Euler-Bernoulli beam with tip mass. According to Courant’s maximum-minimum theorem, maximum value of the first natural frequency of a beam with a single additional rigid internal support, is equal to the second natural frequency of the unsupported beam. In literature, for a cantilever beam without tip mass, the optimum position of intermediate support was reported as 0.7834L and minimum dimensionless stuffiness as 266.9. In this paper, the effect of tip mass ratio on optimum location and minimum stiffness is investigated. The Finite element method is employed. Cross sectional area is uniform and material is homogeneous and isotropic. Numerical results demonstrate that as tip mass ratio increases the optimal position moves toward the tip mass and minimum stiffness increases. For instance, for tip mass ratio 0.5, optimal position is 0.92L and minimum dimensionless stiffness is 284. Optimal position and minimum stiffness are presented for various range of mass ratio. In many applications, it is not possible to place intermediate support at optimal position; therefore, the minimum stiffness does not exist. In these cases, a tolerances zone is considered and related design curves are proposed. As a practical example, an agitator shaft is considered and end impeller is modeled as tip mass. The effectiveness of the proposed design curves in order to maximize natural frequency is shown. A design of an intermediate support is presented; in this example the fundamental frequency has increased as much as 300 percent without any change in shaft diameter.Keywords: Euler-Bernoulli, intermediate support, optimal position, minimum stiffness
-
Pages 133-142Sheet metal assemblies are widely used in the automobile, aerospace, and shipbuilding industries. Sheet metals deform during the manufacturing and assembly process due to their high flexibility. Traditional tolerance analysis approaches were developed for rigid assemblies; however, new approaches of tolerance analysis and variation simulations have been proposed for flexible (compliant) assemblies using FEM. In this paper, a new method called Interactive Worst Case (IWC) is introduced for tolerance analysis of flexible assemblies, which demands a few FEM simulations and is based on traditional Worst Case (WC) method. IWC method guarantees that all the parts will assemble accurately and have proper function. The case study of this paper is two flexible sheets in the form of quarter cylinders, joined together by six spot welding to form a half-cylinder assembly. The accuracy of IWC is verified by comparing the results to uniform MIC. The results of MIC are also compared to the results of the Monte-Carlo simulation (MCS).Keywords: Assembly Spring-back, Compliant Assembly, Interactive Worst Case Method, Method of Influence Coefficients, Sheet Metal Assembly, Tolerance Analysis
-
Mechanical Properties of Materially and Geometrically Gradient Cellular Structures Manufactured with SLS 3D Printer Applicable as a Bone ImplantPages 143-155Cellular structures are broadly used because of their exclusive properties in tissue engineering. This research proposes a new method, both in design and manufacturing, to engineer their mechanical properties considering gradient material and geometrical features and evaluate the possibility of using created structures as bone implants. Schwarz-primitive surface has been utilized to design cellular structures with different porosities and unit cell sizes. A total of 18 cellular structures were designed and fabricated using the SLS 3D printer with a new unconventional approach in adjusting the settings of the machine, and their mechanical properties were extracted. The structures' internal properties were evaluated using the FESEM. Comparing the mechanical compressive test results showed that adjustments in material and geometry improved mechanical properties (such as the compressive moduli, compressive strength, and yield strength). For instance, in 3 mm samples, the elastic modulus in material gradient and geometrical gradient structures is 20% and 73 % higher than the minimum values of the uniform structure. FESEM imaging revealed that adjusting the absorbed energy by powders (controlled by laser characteristics) leads to the formation of natural voids with diameters in the range of 6 to 144 μm for the gradient structures. Evaluation of the designed structures showed that 6 of them (4 uniform porosity and 2 geometrically gradient) have mechanical behavior of the desired tissue. The research outcomes can assist in optimizing manufactured parts by SLS 3D printers with internal and external controlled properties to obtain more desirable mechanical characteristics, especially for tissue engineering applications.Keywords: Additive Manufacturing, Cellular structures, Gradient structures, Selective Laser Sintering, Tissue Engineering, Triply periodic minimal surface
-
Pages 157-166In dynamic model of planetary gears, one of the key design parameters and one of the main sources of vibration is time–varying mesh stiffness of meshing gears. According to previous researches, the finite element method and analytical method are two techniques to estimate the mesh stiffness of meshing gears. In this work, in an innovation the periodically time–varying mesh stiffness of meshing gears is examined by both of finite element and analytical methods. The planetary gear set is modeled as a set of lumped masses and springs. Each element such as sun gear, carrier, ring gear and planets possesses three degrees of freedom and is considered as rigid body. The influence of effective parameters on the mesh stiffness of meshing gears and also numerical results of natural frequencies and vibration modes of the system are obtained. Based on the results, the influence of the higher pressure angles on the mesh stiffness of meshing gears is perceptible. By using the proposed mesh stiffness of meshing gears, for the system with numbers of odd and even equally and unequally spaced planets, natural frequencies and vibration modes are validated with a high accuracy.Keywords: Pressure angle, Meshing gears, Vibration mode, Natural frequency